Types of Printed Circuit Boards
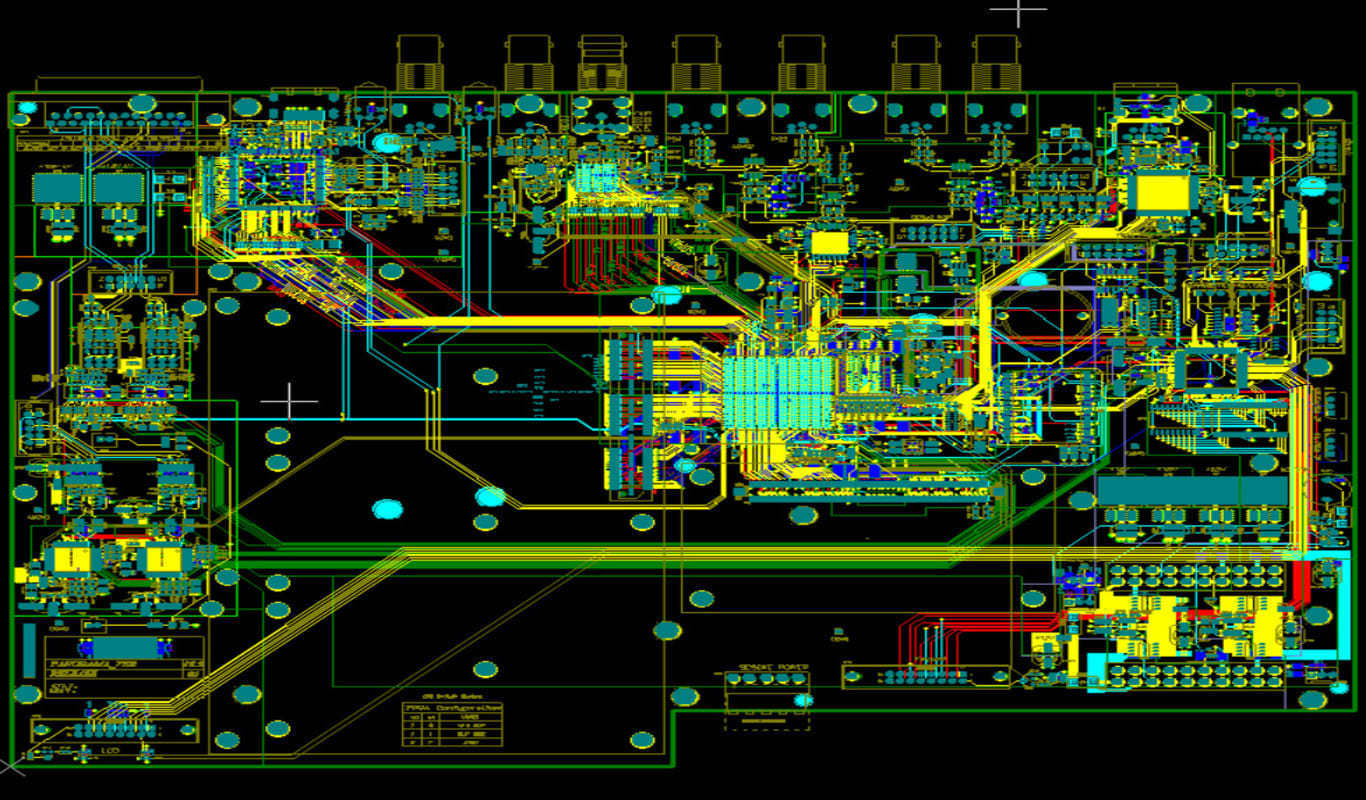
Printed circuit boards are classified into various types based on the manufacturing process, design specifications, and application requirements such as medical, automotive, defense, and space. More complex designs based on consumer needs and requirements paved the way for the manufacture of different types of PCB boards. Before choosing a PCB, you must consider factors such as required space, stress handling, and mechanical and electrical stability. The following articles introduce you to the differences between the different types of circuit boards.
Single-sided PCB
Single-sided PCBs are the most common type of printed circuit board. It has a single conductive copper layer above the substrate. Electrical components are soldered or placed on one side of the board, while the entire etched circuit is visible on the other side. Since these boards have only one conductive layer, the conductive paths cannot intersect or overlap, thus taking up a lot of space.
Therefore, these PCBs are suitable for low-density design requirements. Single-sided printed circuit boards are used for basic and low-cost electrical/electronic instruments such as calculators, power supplies, LED lighting boards, FM radios, timing circuits, and more.
Advantages of single-sided PCB
Cost effective
Easy to manufacture
Suitable for low-density designs
Easy to fix if something goes wrong
Easy to design
Double sided printed circuit board
A thin layer of conductive material, such as copper, is added to both the top and bottom of the circuit board of a double-sided PCB. Holes in the circuit board allow metal parts to be attached from one side to the other. These PCBs use one of two mounting methods (through-hole technology or surface-mount technology) to connect circuits on both sides. Through-hole technology involves mounting leaded components into pre-drilled holes on the board, which are then soldered to pads on opposite sides. Surface mount technology requires the precise placement of electronic components on the surface of a circuit board.
Double-sided PCBs are used in a variety of applications such as cell phone systems, power monitoring, test equipment, amplifiers, HVAC applications, UPS systems, and more.
Advantages of double sided PCB
Reduced size and compact circuit
Relatively low cost
More flexible
Increased circuit density
Suitable for advanced electronic systems
Multilayer PCB
Multilayer PCBs have more than two copper layers. Generally, any circuit board with at least three conductive layers is included in this category. Multilayer PCBs are designed in a "sandwich" fashion, with multiple double-sided conductive layers divided by the same number of sheets of insulating material. All must be bonded and laminated together under high pressure and temperature to ensure that no air gaps exist and that the final PCB assembly is properly stable.
Multilayer PCBs are used in computers, laptops, cell phones, tablets, medical devices, GPS trackers, and many other more complex circuits and devices.
Advantages of multilayer PCB
Small size
More powerful
High level of design flexibility
Suitable for high-speed circuits
Rigid PCB
As the name suggests, a rigid PCB is a circuit board that cannot be twisted or folded. The base material of the board is a rigid substrate that gives the board rigidity and strength. They consist of multiple layers, including a substrate layer, copper layer, solder mask layer, and silk screen layer, which are bonded together by adhesive and heat. While some boards are single-sided, double-sided, or multi-layer, rigid PCBs can be either, depending on the need. However, once made, it cannot be modified or changed.
Rigid PCBs are used in GPS devices, computers, laptops, tablets, cell phones, X-rays, heart monitors, CAT scans, MRI systems, temperature sensors, control tower instruments, and more.
Advantages of rigid PCB
Cost effective
Easy to diagnose and repair
Low electrical noise
Ability to absorb vibration
Pocket
Light
Flexible printed circuit board
A flexible printed circuit board consists of many printed circuits and components arranged on a flexible substrate. Flexible PCBs are usually made of polyamide, PEEK (polyetheretherketone), or transparent conductive polyester film. Flexible circuit board, flexible PCB, flex circuit, and multifunction printed circuit are other names for these circuit boards. These printed circuit boards are made using the same components as rigid printed circuit boards. The main difference is that the board is designed to bend into the desired form throughout the application. These PCBs are available in single-sided, double-sided, and multi-layer configurations. This helps reduce the complexity of unit assembly.
Flexible PCBs are used in Organic Light Emitting Diode (OLED) manufacturing, LCD manufacturing, flexible solar cells, the automotive industry, cellular phones, cameras, and complex electronics such as notebook computers.
Advantages of flexible PCB
Space saving
Eliminate connectors
Thermal management
Improve reliability and repeatability
Provides uniform electrical characteristics for high-speed circuits
Ideal for applications requiring high signal trace density
Rigid-flex PCB
A Rigid-flex PCB is a hybrid circuit board that combines components from flex and rigid circuit boards to form a board that can be folded or continuously bent and is often formed into curved shapes or curves during manufacturing.
Flexible parts of circuit boards are often used for interconnections between rigid circuit boards, allowing narrower conductor tracks to take up less space, resulting in smaller circuit boards. Using flex PCBs for interconnects can often eliminate the need for bulky connectors, making rigid-flex printed circuit boards lighter.
Rigid-Flex PCB design is a little more complicated, as the boards are constructed in 3D, allowing the boards to be folded or twisted to produce the desired shape of the product. Designing circuit boards in 3D enables higher spatial performance, which can then be used in special cases where space and weight reduction are required, such as medical equipment.
Rigid-flex boards can be designed in a compact manner, and their lightweight nature makes them an excellent choice for a wide range of applications in aerospace, medical, and consumer electronics.
The advantages of rigid-flex PCB
360-degree bendability
Reduced space requirements with 3D capabilities
Shock resistance
Improve reliability
Light
Fewer solder joints ensure higher connection reliability
Simplified PCB assembly process
When choosing a PCB manufacturing partner, consider cost optimization, proper material usage, lead times, and more. If you plan to buy circuit boards, please contact us.
Singo is a professional custom PCB board manufacturer. Our company has been specialized in electronic PCB assembly. Mainly engaged in PCB assembly and OEM/ODM electronic manufacturing services since 2006. The products involve home appliances, digital products, industrial control, and medical equipment. After years of hard work, we have established long-term cooperative relations with some well-known international companies.