Single-Sided and Double-Sided PCB
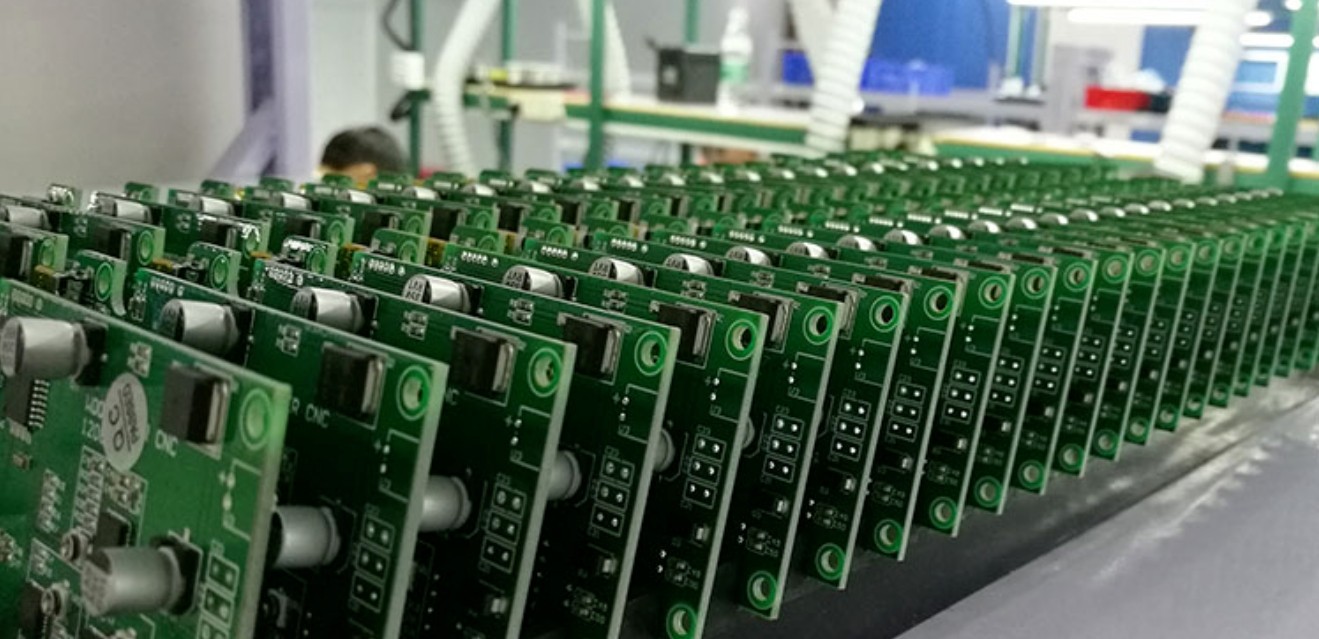
Single-sided boards usually have a layer of copper foil bonded on one side of the substrate, while in double-sided boards, the substrate is sandwiched between two layers of copper foil bonded on both sides. A substrate with two layers of copper foil is also called a copper-clad laminate. Read on to learn more about single-sided versus double-sided PCBs.
Why Do You Need Two or More Layers?
Whether the circuit uses through-hole components or surface-mount components, there is always the possibility that a single-layer board can fully contain it. If the circuit is complex, several jumper wires may be needed to accommodate it. However, for a single-sided PCB, the size of the board may become too large.
As electronic products continue to shrink in form and size, large PCBs can become a hindrance. Adding another layer to make a double panel is like folding the single panel itself. This effectively cuts the size of the board in half while still accommodating the entire circuit. However, both single-panel and double-panel have their own advantages and disadvantages.
Advantages of Using a Single-Sided Board
Simple design
Simple production process
Easy to assemble
Shorter assembly time
Easy to troubleshoot
Disadvantages of Using a Single Panel
Large size is suitable for complex circuits
Low component density
Low mechanical strength
Inability to withstand high levels of vibration
Advantages of Using Double-Sided Panels
Higher component density with vias
Can support complex circuits
Possibility of mixed assembly
Smaller size for complex circuits
Higher mechanical strength
Can withstand higher levels of vibration
Disadvantages of Using Double-Sided Panels
Longer design time required
The production process is more complicated
Longer assembly time
Troubleshooting is more difficult
When to Use Single-Sided or Double-Sided?
The industry prefers single-sided panels because of their simplicity and low cost. Single-sided panels can be less expensive to manufacture and assemble if there is sufficient space inside the device. Due to their simple design, lead times for manufacturing single-sided panels are shorter, resulting in shorter lead times and shorter time-to-market.
However, when the circuit is complex and the number of components is large, the space inside the device may not be able to accommodate a large single-sided board. In this case, double-sided or even multi-layer boards may be required.
Both through-hole and surface-mount components can be used on both types of PCBs. For through-hole components, the PCB must have holes to accommodate long leads. For single-sided boards, the connections for through-hole components are on the bottom of the board. On the other hand, for surface mount components, a single-sided board will have connections on the top side.
When using through-hole components on a double-sided board, the bottom layer provides the connections. However, there can also be additional connections on the top side, with vias connecting the two layers. For double-sided PCBs, surface mount components can be mounted on both sides.
Another advantage of single and double panels is the support for mixed assemblies. Therefore, it is possible to mix through-hole and surface-mount components on the same board. While through-hole components can only be mounted from the top of the board, there are no restrictions when it comes to mounting surface-mount components - surface-mount components can be mounted on the top, bottom, or sides of a double-sided board. However, for single-panel mounting, surface mount assemblies can only be made on the underside.
In Conclusion
There are two factors that mainly determine the use of single-sided or double-sided. One is scale and the other is cost. While a single-sided board is simpler in design and construction, the larger size required to accommodate the entire circuit offsets the cost. For space-constrained designs, double-sided panels may be less expensive, even if the design and construction are more complex. If you want to buy single-sided or double-sided circuit boards, please contact us.
SINGO is a professional custom PCB board manufacturer. Our manufacturing facilities include clean rooms and advanced high-speed SMT lines (Yamaha), fully automatic printing machines, lead-free wave soldering, and fully automatic assembly lines. Our placement accuracy on IC parts can reach ±0.03mm. This means we can handle almost all types of ICs such as SO, SOP, SOJ, TSOP, TSSOP, QFP, GA, and U-BGA. We not only have strong OEM manufacturing capabilities and engineering support, but also have excellent experience in R&D, manufacturing and repair testing.